Taiwanese saddle manufacturer Velo and component producer SRAM have entered into a collaboration focused on sustainability, aiming to repurpose carbon fiber waste from component manufacturing into bicycle saddles. The Show Daily spoke with Velo CEO Ann Chen about the project.
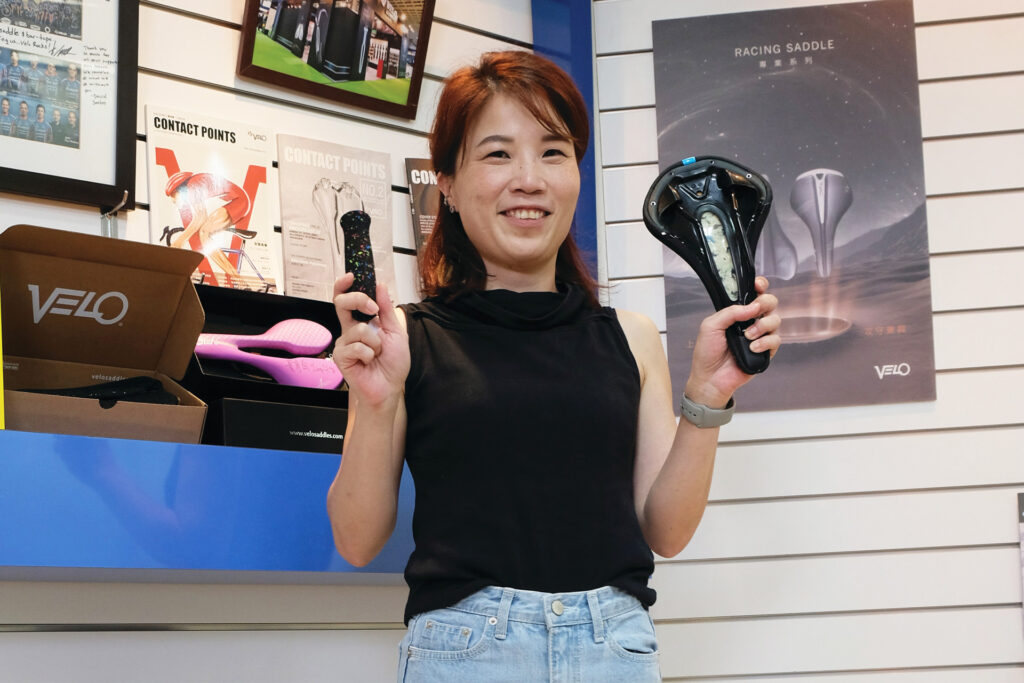
The circular economy has become a widely used term in recent years, fueled by rising global environmental awareness. In this context, two leading companies—Velo, a saddle manufacturer producing around 12 million units annually and component behemoth SRAM—have embarked on a joint project to tackle the challenge of recycling carbon fiber waste from bicycle component production. The goal of the collaboration is to utilize and recycle the carbon fiber waste, generated by manufacturing lightweight components under SRAM’s ZIPP brand.
According to Ann Chen, CEO of Velo, the collaboration emerged naturally through shared sustainability goals and ongoing industry conversations. “The initiation came through many conversations between myself and Bob Chen, General Manager of SRAM Taiwan. We often bump into each other at different seminars on sustainable topics. Both of us are very involved in R&D for our products and production. Therefore, we really wanted to collaborate somehow and came up with this circular economy idea to work together,” she explains in an exclusive interview with The Show Daily.
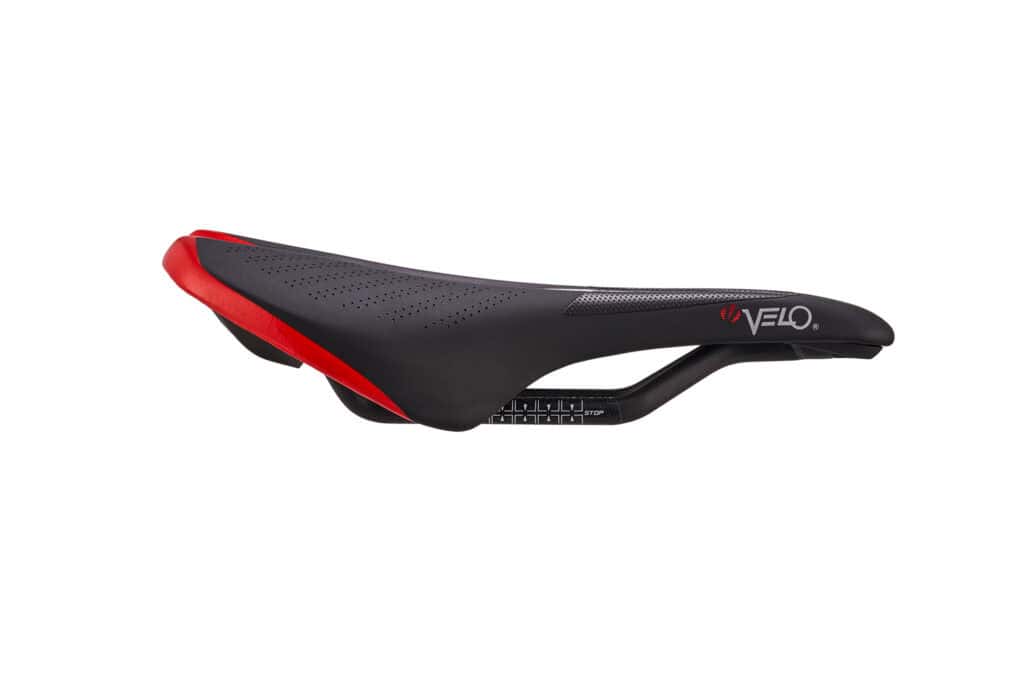
A formula suitable for making performance saddles
The primary challenge was developing a viable formula using recycled carbon fiber suitable for saddle manufacturing. “As we all know, saddles need not only comfort but also must pass very strict tests for functional and safety concerns,” says Chen. “On the other hand, we also know that recycled carbon fibers could be weaker than new ones due to different fiber lengths, and some could be really short. Finding a way to maintain the comfort—the flexibility of the saddles—without adding too many fibers, as fibers create stiffness, while still allowing the saddles to pass the ISO standard, was key for this development. Through many lab tests, we verified a formula suitable for making performance saddles.”
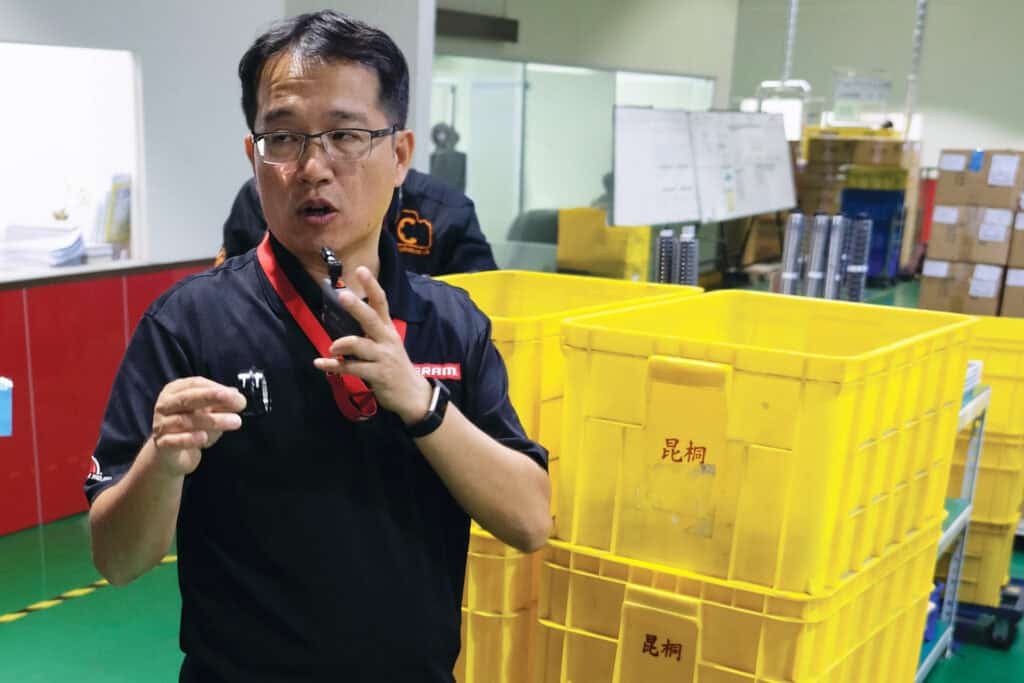
The solution developed by SRAM and Velo blends recycled carbon fibers with nylon, creating a composite material now integrated into Velo’s saddle production. According to Velo, each saddle produced using this composite reduces carbon emissions by approximately 380 to 785 grams, depending on the recycled fibers used. Additionally, the proximity of SRAM’s and Velo’s production facilities in Taiwan, which are less than 20 kilometers apart, has simplified logistics, making their collaboration even more efficient. Chen emphasizes that this newly developed material is not limited to a single product but can potentially be applied across Velo’s entire range of saddles: “It is a formula that we developed together that can substitute our current one. So, we actually can apply this formula to many saddles,” she says.
The partnership underscores the growing importance and feasibility of circular economy practices in cycling, highlighting how collaboration can transform sustainability goals into tangible outcomes. “Both Velo and SRAM really want to do something good for our environment,” Chen concludes. “What people treat as trash—recycled materials—can be regenerated and used at equal value.