From smart factories to AI-driven automation, industrial manufacturing is evolving rapidly. The Show Daily looks at how AI is transforming the bicycle industry.
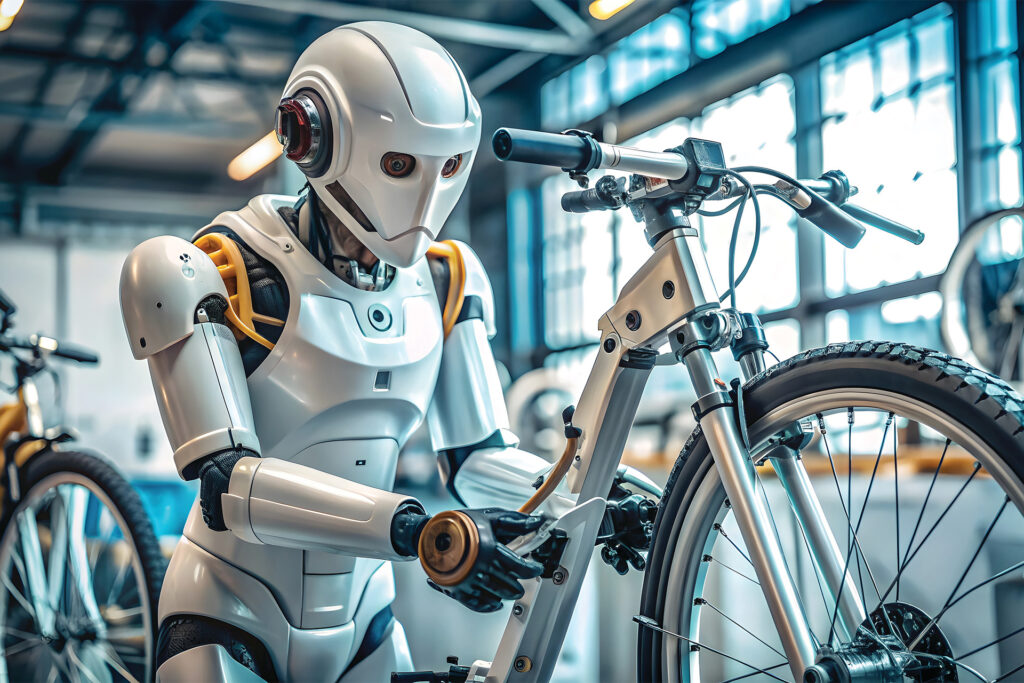
A fully connected e-bike smart factory, where artificial intelligence (AI) orchestrates every aspect of production. Assembly lines run autonomously, with machine learning algorithms optimizing workflows in real time. Robots predict mechanical failures before they occur, automated vision systems detect microscopic defects and AI-powered supply chains adjust dynamically to shifting global demands. This is not a science fiction scenario—it is the emerging reality of modern manufacturing. At last year’s Hannover Messe, Amazon Web Services (AWS)—the cloud computing powerhouse of Amazon—brought this vision to life. Through the lens of a fictional e-bike manufacturer, “AWSome e-Bikes,” the demo showcased how AI-driven technology can help bicycle companies navigate inventory shortages, production challenges and quality control issues. The message of the live demonstration was clear: by combining AI, Internet-of-Things (IoT) applications and cloud computing, manufacturers can build products more efficiently and sustainably than ever before. And the bicycle industry? It’s right in the middle of this AI revolution.
Indeed, the rise of AI in manufacturing is by no means just a footnote or a science fiction scenario anymore. Across industries, artificial intelligence is transforming processes at an incredibly rapid, and often incomprehensible, pace, making them faster and more efficient. Bosch, for instance, integrates AI into automobile component manufacturing to enhance precision and reduce waste. Taiwan’s electronics giant Foxconn utilizes AI-driven robotics to streamline its assembly lines, increasing output while maintaining strict quality control. Meanwhile, Nestlé employs AI for predictive maintenance, reducing downtime in its food production facilities and even uses machine learning algorithms to enhance its recruitment processes. And in the pharmaceutical sector, DeepMind’s AI models accelerate drug discovery, identifying new compounds faster than traditional methods ever could. These examples highlight a fundamental shift: AI is no longer an experimental technology but a critical driver of innovation, efficiency and competitiveness across the global manufacturing landscape. The flip side of the coin: With machines learning, making decisions and solving complex problems, industries—including the bicycle sector—must adapt or risk being left behind.
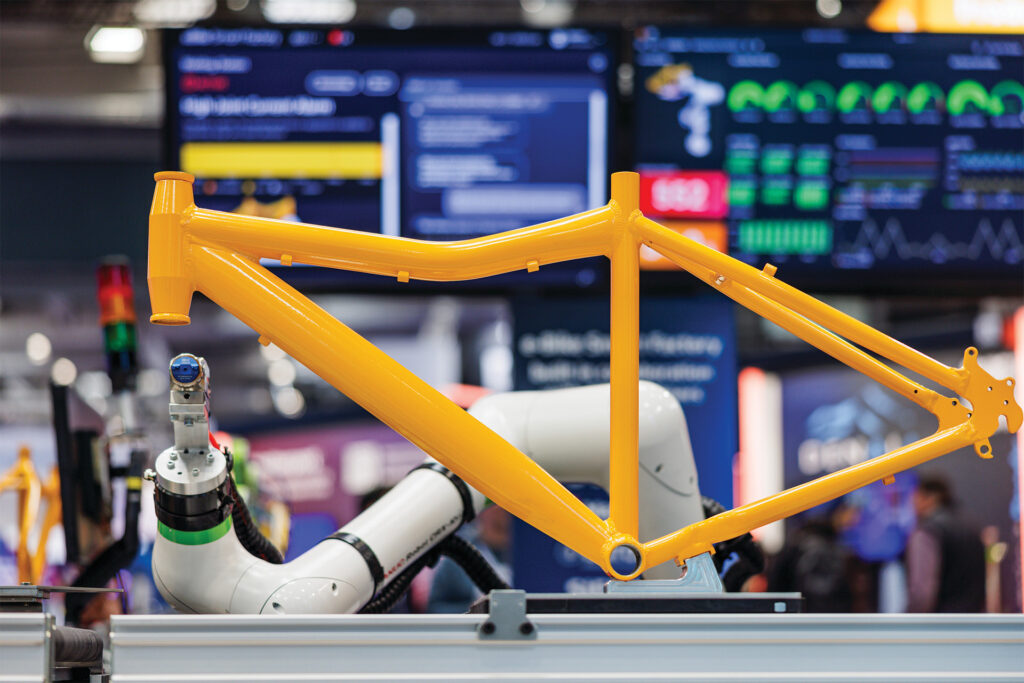
AI-Powered Cobots Reshaping Manufacturing
One company bringing concentrated AI expertise to the bicycle industry is Delta Electronics. Known for its advancements in power electronics—above all, the Delta mid-drive motors for e-bikes—and automation, the Taiwan-based technology giant is making waves in AI-powered collaborative robotics—so-called “Cobots.” Unlike traditional industrial robots, cobots are designed to work safely alongside humans, featuring advanced sensors, adaptive programming and collaborative capabilities that enhance efficiency without the need for physical barriers. “Cobots are already taking on a wide range of tasks in production today. With AI entering this market, new areas of application are likely to emerge, or existing uses may be optimized,” explains Michael Mayer-Rosa, Global Head of Intelligent Robotics Systems at Delta Electronics. “Today, we are at a point where AI is already finding practical applications in many areas, such as ChatGPT or other software that will make our lives easier. At the same time, AI is still in its infancy when it comes to realizing its full potential. However, the current hype is enormous, as AI has the power to fundamentally transform the robotics industry. Many see it as the next major technological revolution, comparable to the advent of the internet,” he adds.
The extent of the changes Mayer-Rosa refers to is well documented in numerous studies. According to research from Statista’s data analysis department, the global number of AI tool users stood at roughly 254.8 million in 2023—more than twice the figure from 2020. Experts predict that by the end of the decade, this number could exceed 700 million. A McKinsey report sheds light on AI’s impact on the labor market, estimating that in the U.S. and Europe, accelerated AI adoption could automate almost a third of working hours by 2030. In the EU, this could rise to 45 percent by 2035. The study suggests that the biggest changes will likely occur in office and administrative roles, but customer service, sales and production will also be affected. “In manufacturing, it’s already clear that major transformations are on the horizon. In our case, our cobots benefit from AI by becoming more intelligent and adaptable, allowing them to take on more complex and dynamic tasks,” Mayer-Rosa says.
The Role of AI in Modern Bicycle Production
A behind-the-scenes look at various exhibitors at this year’s Taipei Cycle Show reveals just how extensively artificial intelligence is already being used in bicycle factories. Giant , for example, employs AI-assisted aluminum manufacturing in frame production. “During the frame cutting and welding process—a critical step in producing a good bicycle—the AI arm can cut the frame with astonishing precision and control each weld run to ensure that the electric motor and battery fit perfectly with the frame,” the company states on its website. Furthermore, “The AI-automated manufacturing process also further improves the quality control of frames. When the solidity of the frame adds extra weight onto the frame itself, the AI arm is still able to quickly and accurately position the frame every step of the way, thereby increasing productivity and ensuring quality.” Notably, AI-assisted aluminum manufacturing is part of a broader initiative aimed at making Giant’s production facilities smarter. “This ensures that our manufacturing processes can stay economically efficient while maintaining excellent quality, precision and flexibility. Moving toward smart manufacturing is a must for industries,” the company adds.
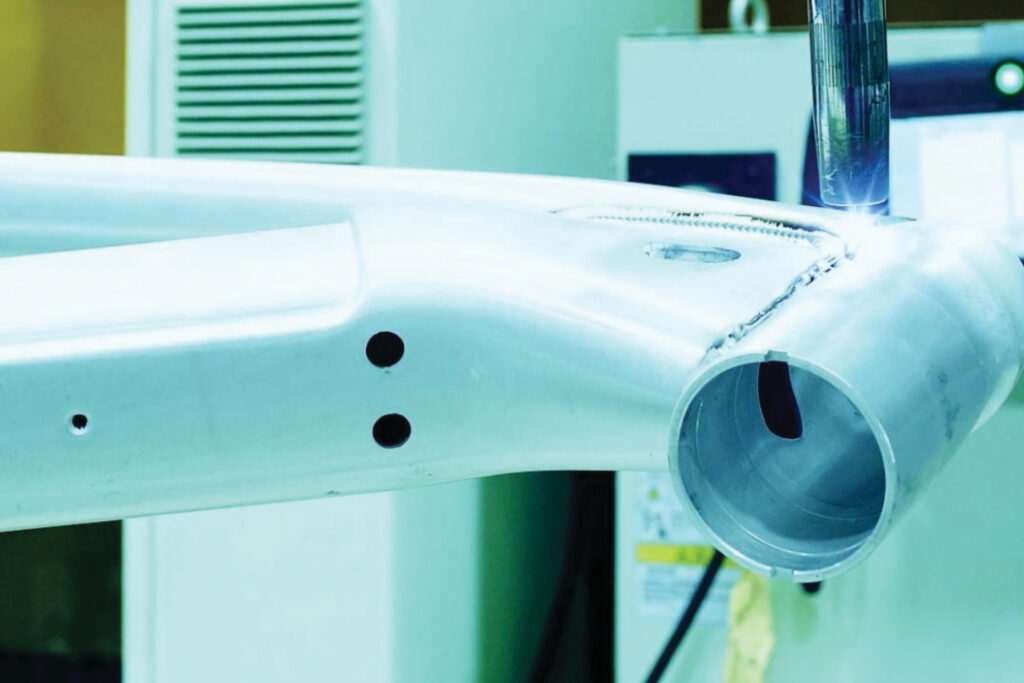
The growing role of AI is also evident among component and accessory manufacturers like Tektro and Nuvo. “At our R&D center, we started integrating AI into our workflows last year. We are currently in the early stages, focusing on using AI language models to assist our electronics control team with design work. Our goal is to enhance the efficiency and completeness of firmware and software design through AI. Additionally, we are exploring how to leverage AI to support the development of project management tools to better handle our growing portfolio of projects,” says Tektro/TRP Marketing Director Otis Chen. The company is also exploring AI-driven improvements in production and warehouse operations, as he reveals: “We are currently discussing and evaluating the implementation of related systems such as MES (Manufacturing Execution Systems) and WMS (Warehouse Management Systems) for the goal of being a smart manufacturing company. Once we start to implement systems like this, we will increase the proportion of AI applications at the factory level,” Chen adds.
How AI Supports Sustainability and Quality Assurance
At Nuvo, AI is being used to reduce energy consumption in production. “Artificial intelligence plays a crucial role in optimization by ensuring a smooth power flow and quickly resolving issues. It also contributes to energy efficiency by learning when heating, cooling and lighting in buildings need to be adjusted,” confirms Marketing Director Amy Shih. The Taiwanese accessory manufacturer is currently building a new factory with the ambitious goal of creating the “first green factory in the bicycle industry.” As a result, the company is closely monitoring advancements in artificial intelligence, Shih adds.
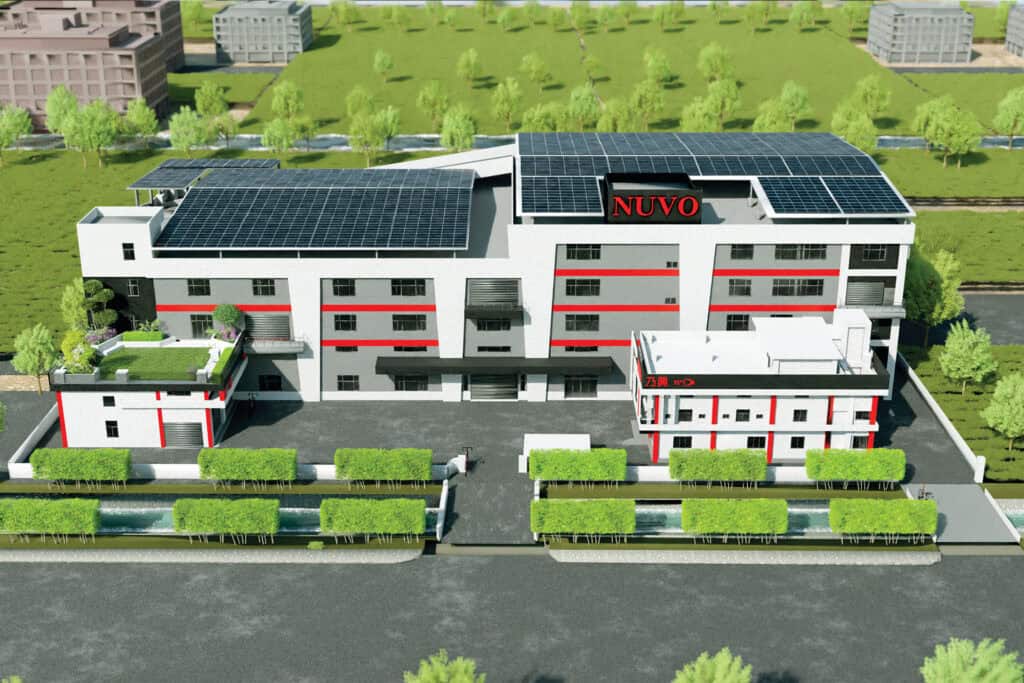
French retailer and bicycle manufacturer Decathlon is also using AI to enhance sustainability in bike production. By 2026, the company aims to cut CO2 emissions from its sold products by 40 percent across all business areas, with 20 percent of these reductions coming from product design alone. To achieve this, Decathlon has partnered with U.S. software company Autodesk, integrating generative AI design into its development process. The goal is to reduce material usage while maintaining or even improving product performance. “We are aware that we are only at the very beginning of an innovative design process,” said Charles Cambianica, Head of Product Design at Decathlon, in a press release sent out at the launch of the project in 2021. “This new approach will fundamentally change how we develop products. We need to see generative design as an opportunity, fully explore its potential and embed it into our design workflow because that’s where we can make the biggest ecological impact,” he added.
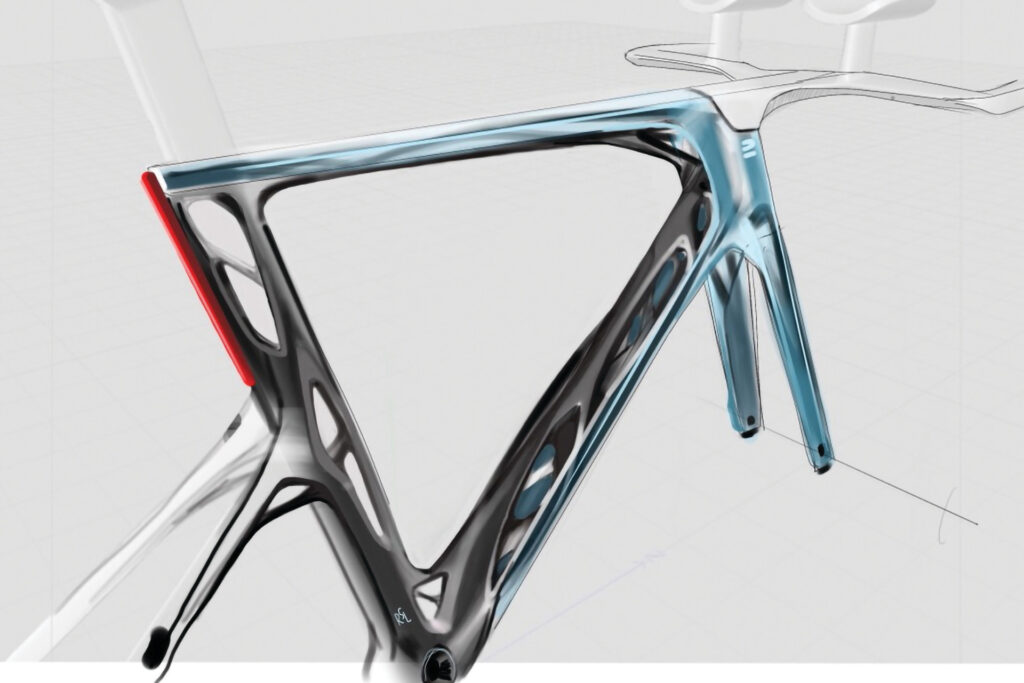
Artificial intelligence will also play a crucial role in quality assurance within production—early examples from the bicycle industry already demonstrate this. Since last year, German drive unit specialist Porsche Ebike Systems has been using the AI-powered acoustic testing software “Sounce.” This software analyzes characteristic structure-borne sound patterns of various components in Fazua Drive Units and detects deviations in real time. “This application thoroughly examines all potential sources of error—including gearbox, bearing, assembly and electronics deviations, as well as contamination of individual components—and documents any defects,” explains Florian von Wurmb-Seibel, Chief Technical Officer at Porsche Ebike Performance. The result of its implementation: quality assurance cost efficiency increased by approximately 60 percent. “The bicycle industry may not be a pioneer in artificial intelligence, but thanks to its agility, it can quickly implement value-creating innovations. With this in mind, we are convinced that AI will become increasingly visible in our industry in the near future,” he says.
A Glimpse into the Future of Bicycle Manufacturing
From optimizing production processes and product design to enhancing quality assurance and sustainability, artificial intelligence is already reshaping the bicycle industry in profound ways. While widespread adoption is still in its early stages, pioneering companies are demonstrating AI’s potential to revolutionize the sector. The benefits are clear: AI can streamline operations, reduce costs, improve efficiency and elevate both product quality and customer satisfaction. Therefore, the AWS demonstration at Hannover Messe offered a striking glimpse into this future. The fictional “AWSome e-Bikes” factory was more than just an exhibition centerpiece—it was a real-time simulation of how AI-powered factories will operate in the coming years. It was a clear statement that smart factories are no longer a futuristic vision but an imminent reality, with AI poised to drive the next wave of industrial efficiency and sustainability.