As the supply chain for bicycles in Vietnam grows, SR Suntour is expanding its footprint in the country’s South by adding a second facility and producing more parts in-house.
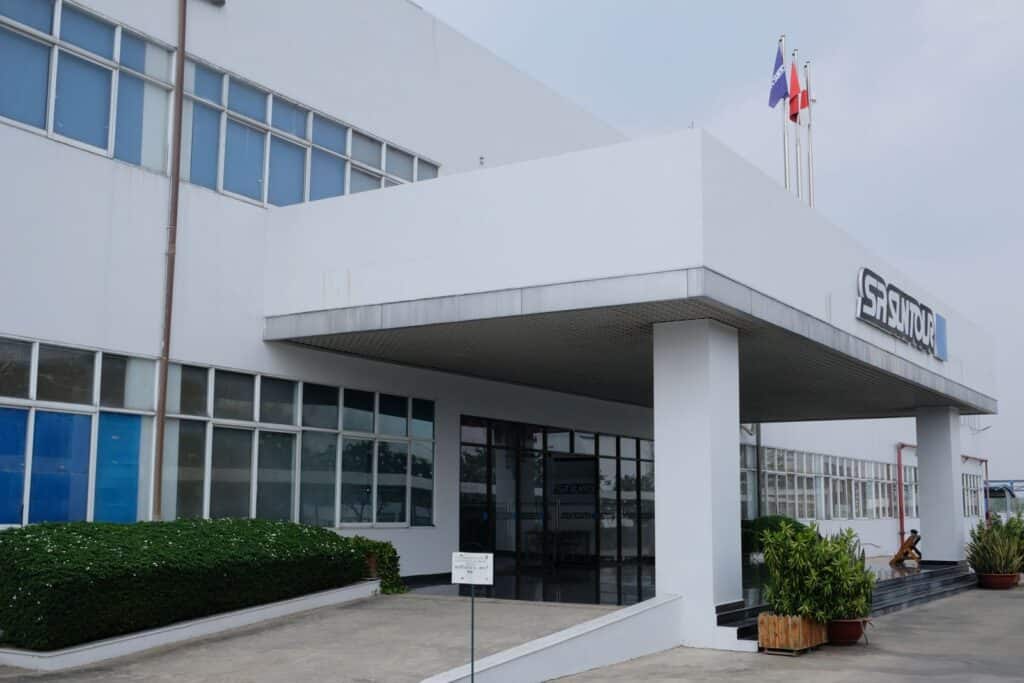
With a line-up ranging from simple entry-level forks to Olympic gold medal winning models and a strong position in the OE market, SR Suntour is a key supplier to the bicycle industry. Operations in Ben Cat’s Protrade Industrial Area started in 2017, focusing on suspension forks with alloy lowers, suspension seat posts and e-drive systems with hub motors. With a footprint of 50,000 m2 this factory has a staff of around 500 focusing on casting, painting and assembling. The machinery used is quite impressive as well: additional alloy casting lines have been installed to produce alloy parts. Magnesium casting however is being done at SR Suntour’s Taiwan factory only. Since suspension forks with alloy lowers are positioned in the entry- to mid-level segment, the fork output is mainly supplied to assemblers and customers in Southeast Asia.
The SR Suntour Vietnam factory is tailored for volume
“SR Suntour’s Vietnam factory is clearly tailored for volume, so any issues need to be identified quickly to avoid producing goods that do not pass quality control and end up as scrap,” explains Vice General Manager Roderick Wang. “Our quality control in Vietnam mirrors those at our factories in Taiwan and China. It is not restricted to incoming and finished goods but also monitors every step throughout the production.” The existing factory saw equipment being added during the pandemic cycling boom with an additional painting line. When demand dropped, SR Suntour reacted quickly and started throttling its production in Vietnam in the fall of 2022. Having gone through similar industry downturns in the past, the company’s management were ready to respond appropriately.
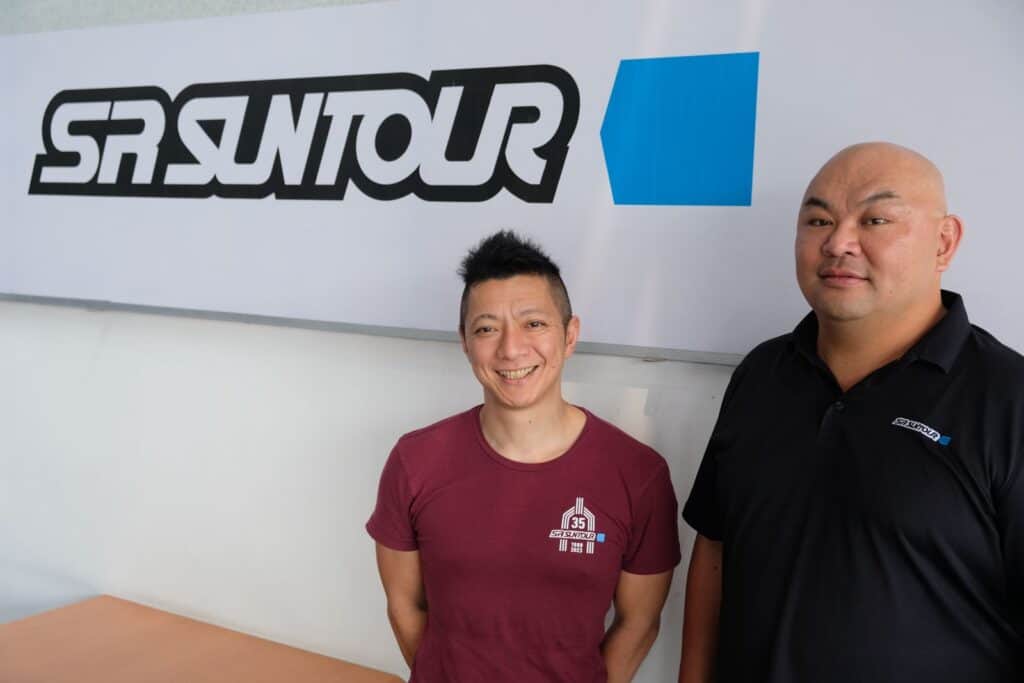
Second factory ensures increased production capacity
In an effort to spread its production capacity across multiple countries and thus reduce exposure to external risks, SR Suntour has been expanding its footprint in Vietnam by renting a second factory up the road in the same industrial area. At 60,000 m2 this factory is slightly larger than the first one. Apart from two warehouses for forks and hub motors, it will be outfitted with yet more casting lines for alloy parts. The production of various tubes will also be brought in-house once this second factory has become fully operational – which should be the case by 2025. “Our in-house production offers big advantages in terms of end-to-end quality control and to get the origin of parts certified, which is an important aspect given ongoing trade conflicts and the resulting tariffs that we can avoid when producing in Vietnam,” according to Wang.