Swiss start-up 9T Labs traveled to Taichung Bike Week with a novel idea. The lab is working on ways to combine additive manufacturing and injection and compression molding to speed up the production of serial structural composite parts.
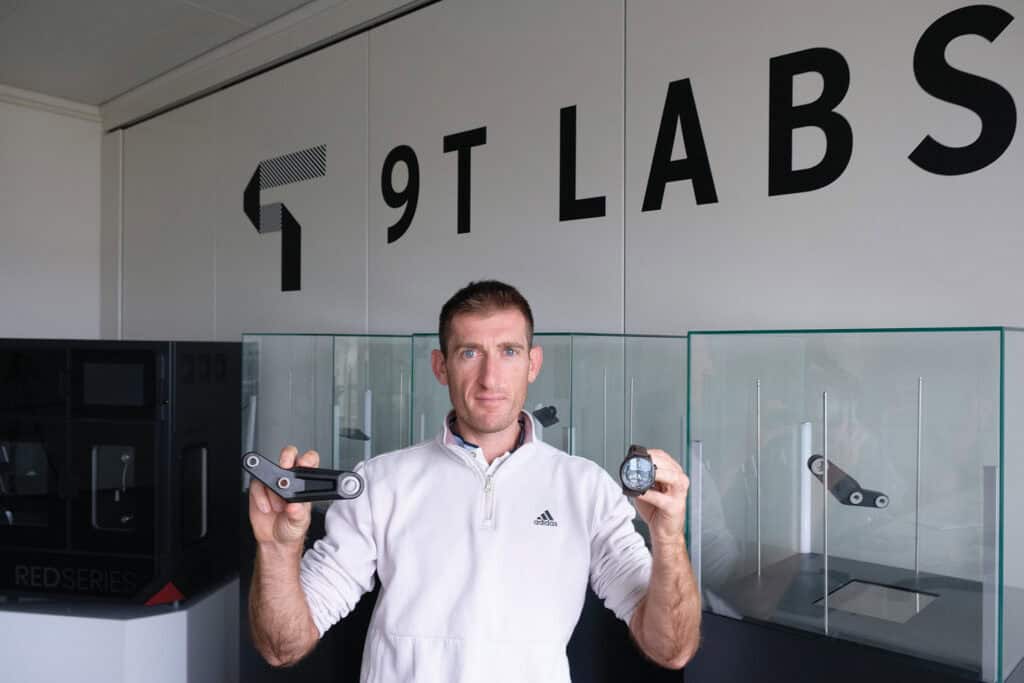
While additive manufacturing is getting more popular within the bicycle industry, no real scalable solution has emerged yet to speed up production and bring down costs. Young Swiss company 9T Labs wants to change this by combining novel technology with injection and compression molding as a proven production method.
“Basically, we build the core of any part by depositing continuous strands of carbon fiber tapes cut to a narrow, 1-millimeter width in an automated process. As a next step, we add short-fiber composites through injection and compression molding using a separate machine,” 9T Labs’ Director of Business Development Yannick Willemin explains. “This allows for a faster production, very tight tolerances and an optimized use of materials, resulting in either stronger or more lightweight parts when compared to traditional duroplast constructions.”
9T Labs’ business model is not restricted to the bicycle industry
The business model of 9T Labs is quite unique and not restricted to the bicycle industry. Aiming for a close partnership with customers, the company first validates the original design at hand and then writes the code needed to get it produced using continuous strands of thermoplastic composite tapes. Next, the final shape is achieved through injection and compression molding. While small batches can be produced at 9T Labs’ headquarters based on the outskirts of Zurich, the company prefers to sell a starter set including the software, its Build Module and the molding machine.
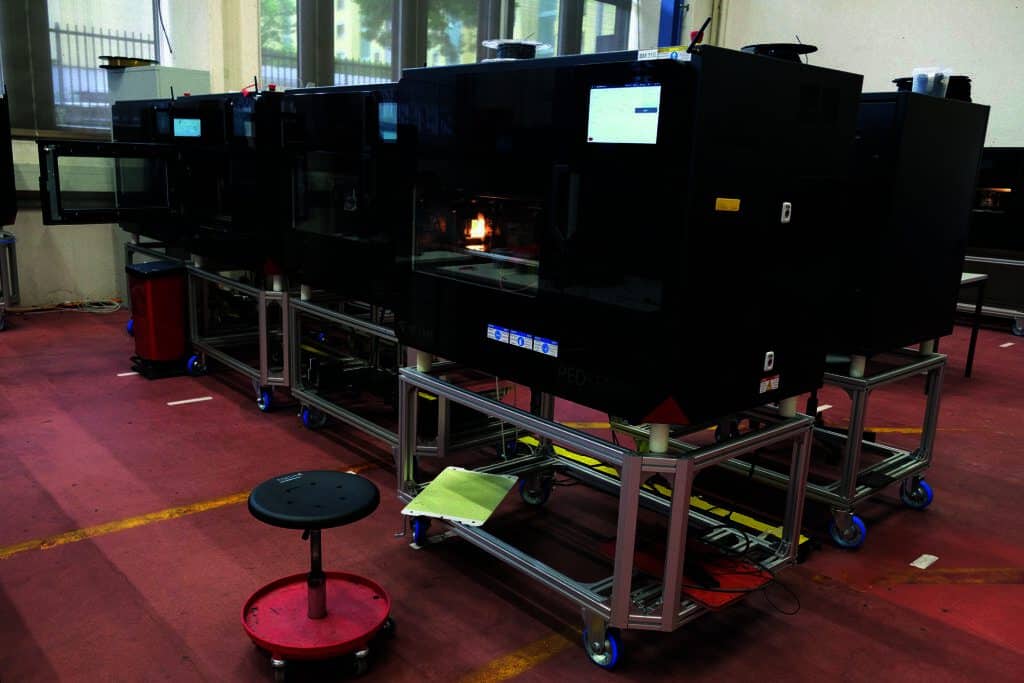
The first forays into the bicycle industry are focused on rocker links for full-suspension frames, either solid or hollow crankarms and other parts, with the first scheduled to hit the markets in the 2026 model year. “The 9T Labs team at Taichung Bike Week had already physical samples ready for product managers, and we also explained our business model that involves training customers to operate our own-designed machines at their facilities,” Willemin said.
Production volume of up to 100,00 units per year
“Scale-wise the sweet spot for our production method likely is at between 1,000 and 100,000 units per year. We aim to find high-tech ways to work with composites, reducing the need for human labor and the amount of scrap, while making steps toward a more sustainable circular economy,” he added.
The first commercially available products from 9T Labs were limited runs of watch housings made of composite materials for Swiss premium watchmaker Oris. Apart from bicycle parts, the Swiss start-up is looking to expand into consumer electronics and aviation, where precision, reliability and low weights are paramount.