Taiwan maker invests heavily to meet e-bike demand
A-Forge [Eurobike hall 9.1 / F30], a leading supplier of aluminum parts for bicycle frames, has announced a significant expansion in Vietnam. Modern bicycle frames come with a lot of parts that are complicated to produce – from oversized down tubes that hold batteries to motor brackets and dropouts for thru-axles. As an aluminum specialist, A-Forge has been a driving force in this area and with its latest substantial investment in Vietnam, the company has further extended its capacity.
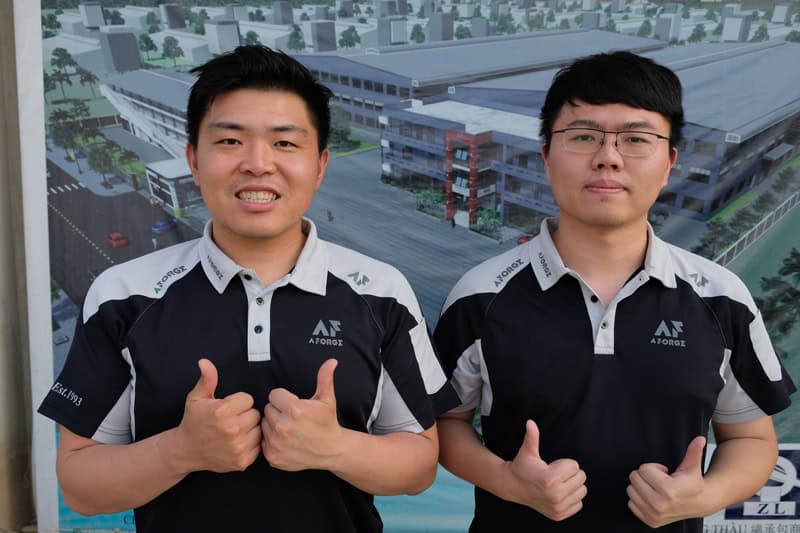
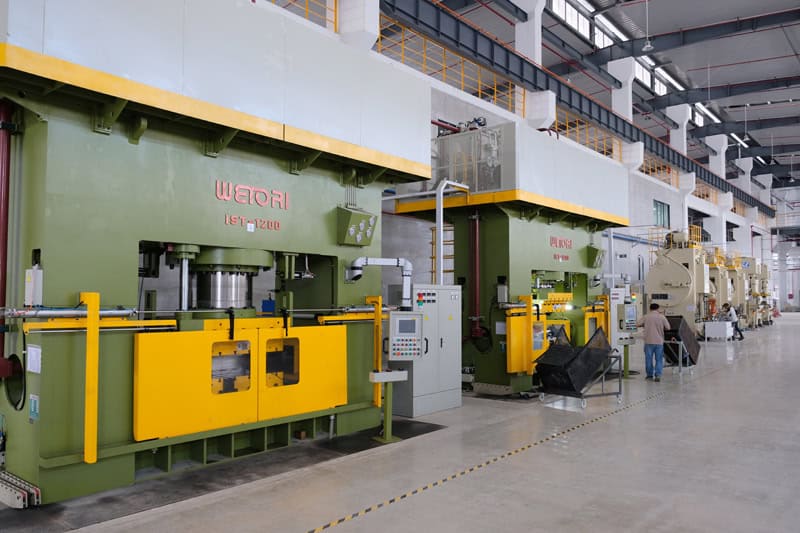
The rise of e-bikes has transformed the bicycle industry, impacting everything from supply chains to frame construction. Modern e-bike frames are a far cry from their welded tube predecessors.
Rather than simply welding standard tubesets together or relying on lugs as connecting parts, modern e-bike frames feature a lot of intricately shaped parts that offer clean and integrated looks and functionality. And while carbon frames may be popular in the upper end of the market, the vast majority of e-bike frames are still made from aluminum. Those frames feature a mix of castings, forged parts and hydroformed tubes. A key player in supplying these alloy parts to frame builders is A-Forge, founded in 1993 by George Chang, who previously worked for Falcon.
A key moment in the A-Forge story is the day George Chang saw an e-bike from Swiss pioneer Flyer for the first time. It only took a short spin for Chang to realize how electric assistance drives could get older or less fit people on bicycles, thus expanding the market for bicycles significantly. As a businessman, Chang also foresaw the changes in frame construction needed for electrification and the resulting business opportunities. From there, things moved fast: A-Forge began supplying both Giant and Merida with alloy parts to build frames and became a supplier of almost every top-tier maker of aluminum frames in Asia. To keep the distances short, A-Forge built no less than five factories in China, always close to key customers.
As electrification took the bicycle industry by storm and branched out into more and more segments – think e-mountainbikes and e-roadbikes –the business of A-Forge grew by a healthy 20 percent year on year. But by 2015 trade conflicts with both the United States and the EU and the resulting tariffs started to cut into China’s competitiveness. As a result, many Taiwanese companies looked to invest in the south of Vietnam. Again A-Forge aimed to keep the distances short. In 2017, George Chang bought a plot of land measuring 24,000 square meters in the Binh Duong province, north of Ho Chi Minh City. He tasked his son Kenith with managing the construction and set-up process which encountered delays due to the Covid pandemic and increasing red tape.
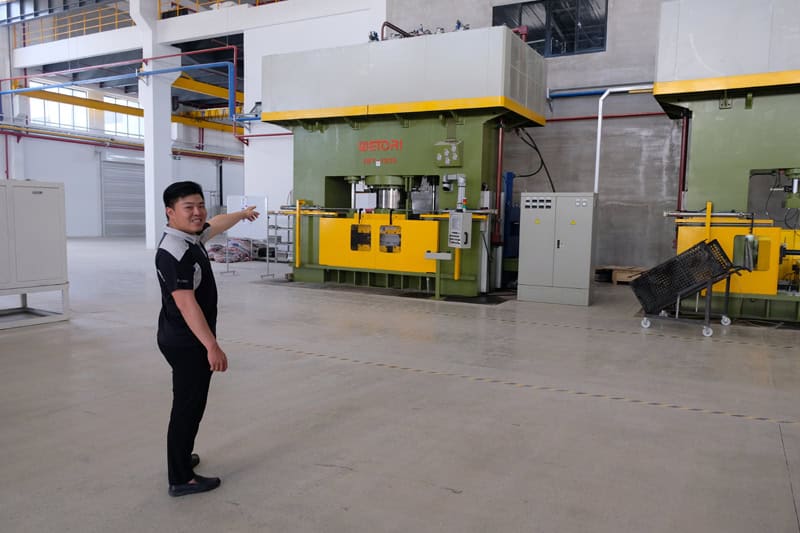
With one hall dedicated to gravity casting and the other housing machines ranging from simple tube benders and hydraulic presses to cold and hot forging lines, 1200-ton hydroforming presses and tapering and butting stations, A-Forge’s Vietnam factory is a one-stop-shop for all things aluminum. Other steps performed in-house include CNC machining, heat treating, deburring and sulphurizing and an automated saponification line has been set up as well. “By performing as many steps as possible in-house, we can apply stricter quality controls at every step and reduce lead times as well,” A-Forge Vietnam general manager Kenith Chang explained when the Show Daily visited the facility earlier this year. “The machinery for gravity casting should be installed by September, and we are also adding another 15 CNC lathes this spring.”
Following the larger trend within the bicycle industry, A-Forge is also keenly aware of ESG matters and is shrinking the eco footprint of its Vietnam production. “We have our own waste water treatment, and the well-insulated roofs have been built strong enough to install solar panels. We also train employees to perform different tasks within the factory so their work will be less monotonous. Robots are mainly used for efficiency and consistency reasons,” said Chang.